Welcome to Day 1 of the Foxboro Pouch Sew Along!
I’m so excited that you want to make the Foxboro Pouch with me! I originally posted these Sew Along tips and tricks in January 2025 in conjunction with a Sew Along I hosted. I’m posting the daily assignments and bonus tips here to my blog for those who didn’t get a chance to join the Sew Along. You can find the Foxboro Pouch pattern HERE and follow along with the Sew Along Blog posts to make your own!
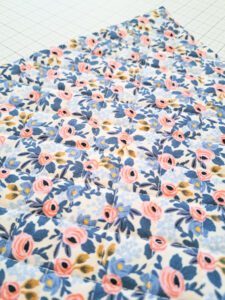
The assignment for the Foxboro Pouch Sew Along Day 1 is to cut everything out, then baste and quilt the Main and Lining fabric. Cutting everything out is pretty self explanatory, but I did want to mention a couple things. First, all of the Accent Fabric pieces can be cut from one square of fabric (as explained in the Cutting Instructions), but feel free to mix in other prints if you desire! You are definitely not required to keep to one print for all of the Accent pieces. Second, if you are using a directional fabric for your Main print, turn to page 10 for instructions on how to get your print facing the right direction (remember, it might take more fabric than a 10″ or 12″ square if you have directional fabric).
One other note before we start: Whenever I’m quilting fabric for a bag, I almost always start off with a bigger size than necessary, then trim to size after quilting. The process of quilting often shrinks the panel (the denser the quilting, the greater the shrinkage), and sometimes the layers shift a little, too. The extra size is always built into my patterns, so no need to cut even larger than the Cutting Instructions given.
Now, on to basting our fabric!
PREPARE FOR BASTING
Before I start basting, I try to make sure that all of my layers are pressed really well. This will help everything lay smoother and you’ll be less likely to get puckers in the fabric when you quilt.
I’d even recommend pressing the batting or Soft and Stable (or other foam stabilizer–unless it’s fusible!) before layering. Both batting and Soft and Stable press well and having the wrinkles pressed out will really help all the layers stay flat.
BASTING
Basting is a way to temporarily hold layers of fabric together. We don’t want the layers to move around while we’re quilting, so we baste them for the best results.
There are many different methods of basting (pins, adhesive spray, sewing long stitches, etc.). I’d recommend trying a few out so you can figure out which method you like best.
I prefer to spray baste smaller projects with Odif 505, but I frequently use safety pins for larger projects.
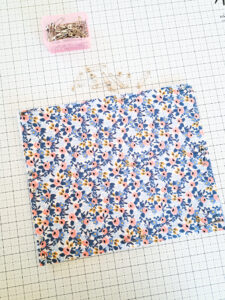
PREPARE FOR QUILTING
Once I have my layers basted, I choose a side of the panel that I can start most of my quilting lines from and stitch a line along one of the edges (just 1/8″ away from the raw edge) to stabilize the three layers.
Even though we’ve already basted, if you start your machine quilting from that stitched line as much as possible, it will further help keep the layers from shifting.
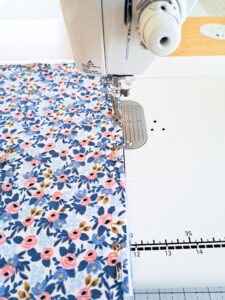
MARKING QUILTING LINES
When I’m quilting a design that needs guides to follow, I like to use a Hera Marker to mark my lines (it only leaves an impression-not an actual ink mark). The dull side of a butter knife also works great! The impressions on some fabrics and batting/Soft and Stable combinations show up better than others, so don’t get discouraged if the lines are a little hard to see. Sometimes I’ll mark and quilt from the lining side if the Hera Marker works better on that side than the main fabric side.
There are many other ways to make guide lines (air/water erasable pens, strips of tape, etc.) or forgo the lines altogether and choose an organic design that doesn’t need lines to follow. If you’d like to see some of these other method in action, check out the video I shared on my Instagram account HERE.
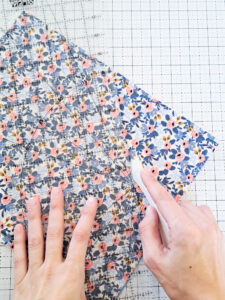
QUILTING
To keep things easy when I quilt, I use the same thread and needle that I use for all of my general sewing projects (my thread of choice is Aurifil 50 wt and I like to use Organ 90/14 needles).
For machine quilting, I do like to increase my stitch length a little. A standard stitch length on my machine is 2.5 and I like to increase it to about 3.5 for quilting. You can play around with your machine’s settings to see what you prefer.
When quilting on my Juki sewing machine, I use a slim presser foot to quilt smaller projects. The Juki comes with a walking foot, however I’ve found that it doesn’t work really well (one of the machine’s only downfalls) and I prefer to use a regular presser foot. If I’m quilting a larger project then I get out my second machine (a Bernina) and use it with a walking foot. The walking foot can really help feed the layers through at the same speed and avoid puckering. If you have a walking foot, I’d generally recommend using it to quilt, or at least trying it out to see if it works better for quilting.
For this Foxboro Pouch, I’m quilting a crosshatch design, using the 45 degree lines on my ruler. If you’re wanting some additional ideas for easy machine quilting designs, check out the Instagram video I posted HERE.
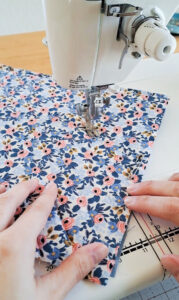
TRIM THE QUILTED PANEL
When you’re finished quilting, trim your quilted panel to the size listed on page 4 of the Foxboro Pouch pattern.
Those are my tips for Day 1! You can find the video to go along with Day 1 of the sew along on my Instagram account HERE.
Links for products from today’s tips:
Odif 505 Spray (click HERE)
Oliso Iron (click HERE)
Juki TL2000 Sewing Machine (click HERE)
Olfa Ruler (click HERE)
Hera Marker (click HERE)
Organ 90/14 needles (click HERE)
Thanks for sewing along with me!
Kristina